Ten techniques for effective inventory analysis, including gathering accurate data, ranking items based on value and categozising items using ABC analysis.
Are you tired of stockouts and excess inventory plaguing your business? Do you struggle with balancing customer demand with the costs of carrying inventory?
It's time to take control with the power of inventory analysis! This guide will dive into optimizing your stock of products or services using ten powerful techniques.
Get ready to unlock the secrets that will revolutionize your inventory management, streamline your operations, and let us assist you in taking your business to new heights of success.
Get ready to transform how you handle inventory. Watch your profits soar as you master the art of inventory analysis!
What Is Inventory Analysis?
Inventory analysis refers to examining and evaluating various aspects of a company's inventory to gain insights into its performance, efficiency, and overall health.
It involves the systematic review of inventory data, such as stock levels, turnover rates, costs, and other relevant factors, to make informed decisions and optimize inventory management strategies.
The goal of inventory analysis is to gain a comprehensive understanding of the inventory's composition, movement, and financial impact on the business.
By conducting this analysis, companies can identify areas of improvement, make data-driven decisions, and implement strategies to optimise stock levels, reduce costs, and enhance customer satisfaction.
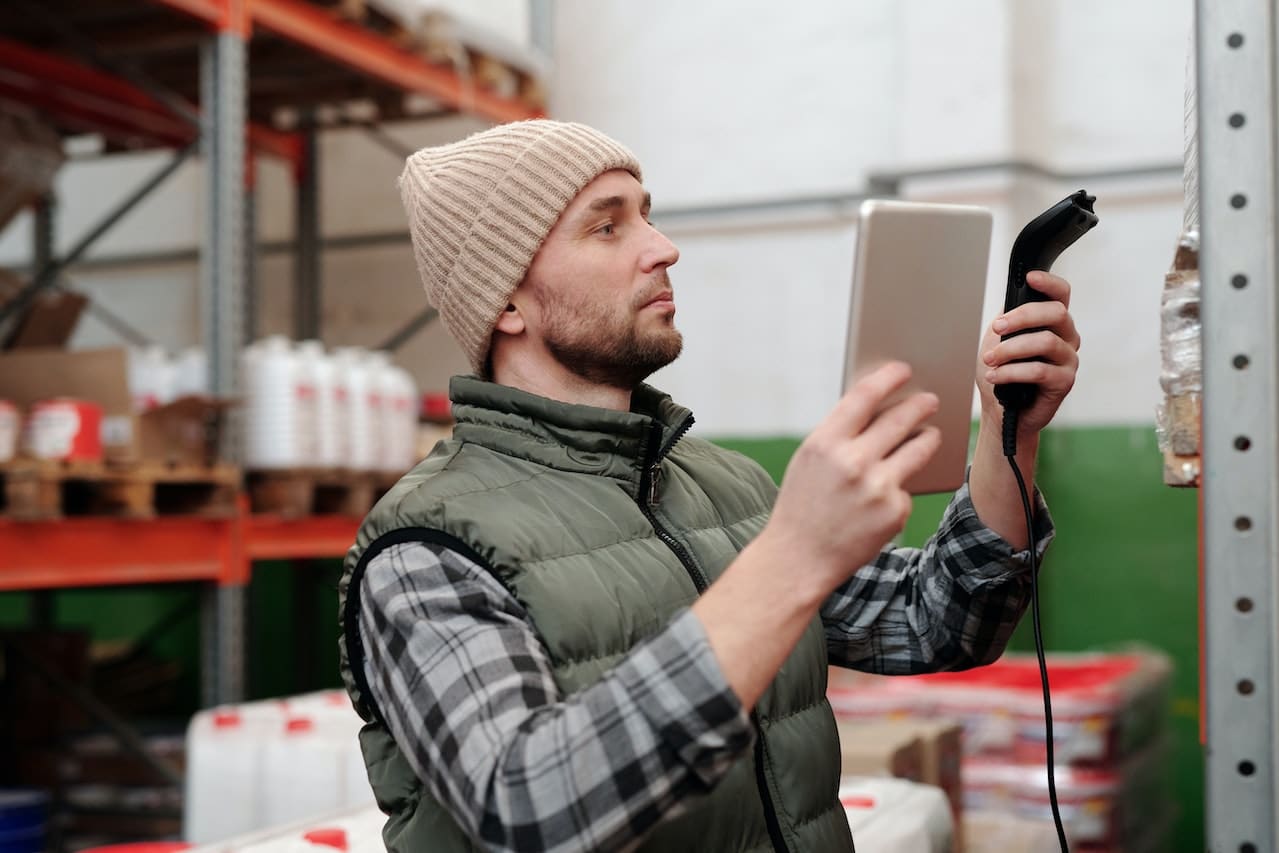
What Are The 9 Types of Inventory?
When managing inventory, it's important to have a clear understanding of various types of inventory is essential for efficient operations.
Inventory serves as the lifeblood of businesses, representing the stock of goods or materials that facilitate production, sales, and customer satisfaction.
However, not all inventory is created equal. It can be classified into different categories based on their characteristics and purpose.
1. Raw Materials
These basic materials and components used in the production process have not undergone any processing or transformation yet. Raw materials are typically purchased from suppliers and are essential for manufacturing or assembling the final products.
2. Work-In-Progress
Work-in-progress inventory includes partially completed products that are still in the production process. It represents the value of materials, labor, and overhead costs invested in the products that have not been completed yet.
3. Finished Goods
Finished goods inventory consists of fully completed products ready for sale to customers. These end products have passed through all stages of the production process and are awaiting delivery or distribution.
4. Maintenance, Repair, and Operations Inventory (MRO)
MRO inventory comprises items and supplies used to maintain, repair, and operate equipment, machinery, and facilities within a business. These can include spare parts, lubricants, cleaning supplies, tools, and other consumables to keep operations running smoothly.
5. Merchandise Inventory
Merchandise inventory refers to the stock of goods that retailers or wholesalers purchase for resale. This type of inventory is commonly found in businesses such as retail stores, e-commerce platforms, and distribution centers.
6. Consignment Inventory
Consignment inventory is a type of inventory that is still owned by the supplier but is placed in the possession of a retailer or distributor for sale. The supplier retains ownership until the inventory is sold, at which point they receive payment from the retailer.
7. Transit Inventory
Transit inventory, also known as pipeline inventory, is the inventory that is in transit between different locations within the supply chain. It includes goods transported from suppliers to the company's facilities, between company locations, or from the company to customers.
8. Seasonal Inventory
Seasonal inventory refers to specifically purchased or produced to meet anticipated demand during specific seasons or periods. This type of inventory is common in industries such as fashion, holiday goods, and agricultural products.
9. Excess Inventory
This type of inventory consists of items that are no longer in demand or have become obsolete due to changes in technology, design, or customer preferences.
Excess inventory refers to stock that exceeds the current or anticipated demand and may require special sales or disposal measures.
What Is Inventory Data Analytics?
Inventory data analytics refers to collecting, analyzing, and interpreting data related to inventory to gain insights and make informed decisions.
It involves applying various statistical and mathematical techniques to inventory data to uncover patterns, trends, and relationships that can improve inventory management and operational efficiency.
Inventory data analytics involves working with large data sets, including information on stock levels, turnover rates, lead times, customer demand patterns, supplier performance, and other relevant metrics.
By leveraging these data analytics techniques, businesses can identify areas for improvement, optimise inventory levels, reduce costs, and enhance customer satisfaction.
Key Performance Indicators (KPIs) are important metrics used to measure and evaluate the performance and effectiveness of inventory management.
KPIs provide a quantitative measurement of various aspects of inventory, enabling businesses to track progress and make data-driven decisions. Some common inventory KPIs are mentioned below.
1. Inventory Turnover
This metric calculates how quickly inventory is sold or used within a specific period, indicating the efficiency of inventory management. To calculate it, you need to divide the cost of goods sold by the average inventory value.
2. Gross Margin Return on Inventory Investment (GMROI)
GMROI measures inventory profitability by comparing the gross margin generated with the average inventory investment. It helps evaluate the effectiveness of inventory in generating profits.
3. Stockout Rate
This metric measures the frequency or percentage of stockouts, which occur when inventory is unavailable to fulfill customer demand. It reflects the ability of the business to meet customer needs and indicates potential lost sales opportunities.
4. Carrying Costs
Carrying costs represent the expenses of holding inventory, including warehousing, storage, insurance, depreciation, and obsolescence. Tracking and analyzing these costs helps identify areas for cost reduction and efficiency improvements.
5. Fill Rate
Fill rate measures the percentage of customer orders that can be completely fulfilled from available inventory. It reflects the ability to meet customer demand promptly and accurately.
6. Lead Time
Lead time measures the time taken to replenish inventory from suppliers. Analyzing lead time helps optimize inventory levels, reduce stockouts, and improve supply chain efficiency.
7. Backorder Rate
The backorder rate measures the percentage of orders that cannot be fulfilled immediately and are placed on backorder. It indicates the level of customer demand that is not met due to insufficient inventory and helps identify areas for improvement in supply chain management.
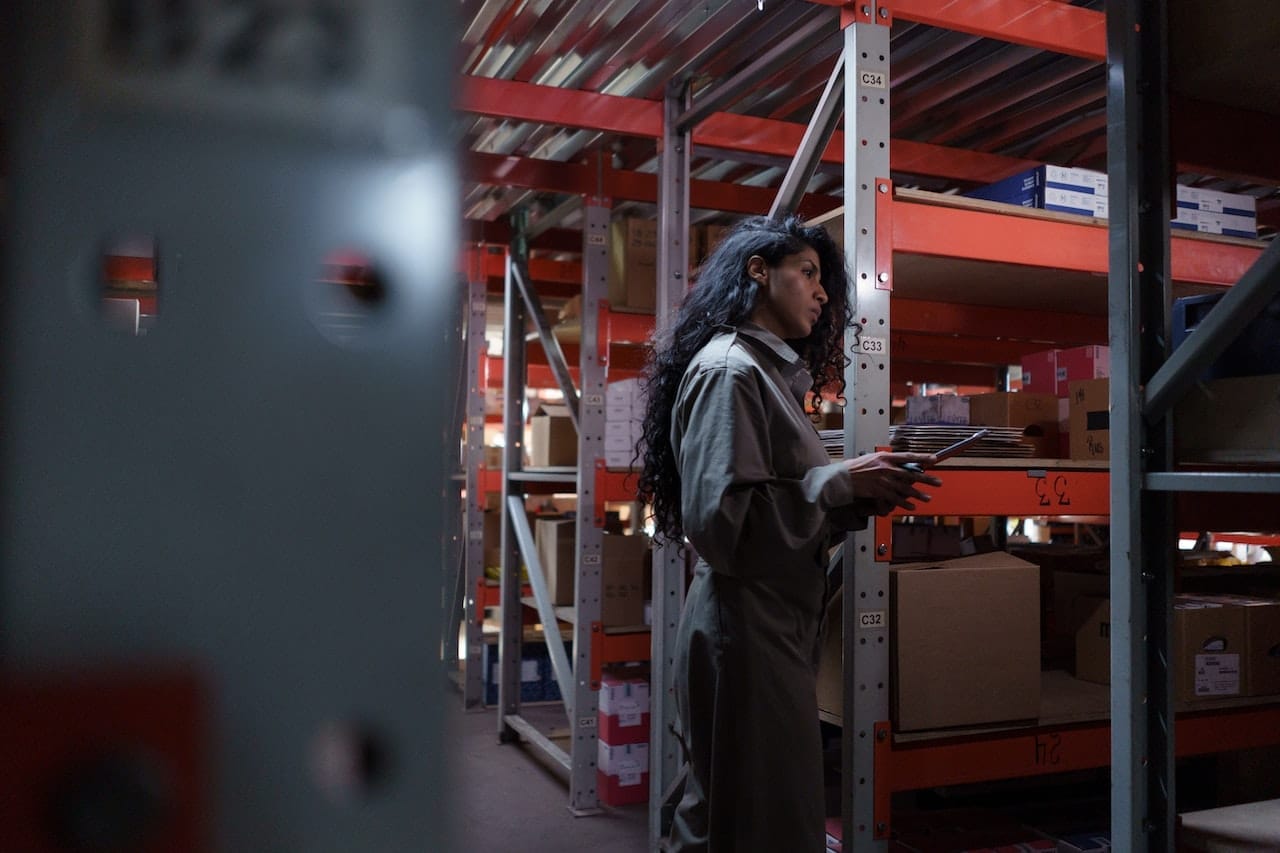
How To Do Inventory Analysis Using ABC Technique
Inventory analysis involves using various techniques to examine and evaluate inventory data to gain insights into its performance and optimize inventory management.
One commonly used technique is ABC analysis, which categorizes inventory items based on their value or importance. Here is a step-by-step guide on how to perform inventory analysis using ABC analysis in inventory management:
1. Gather Inventory Data
Collect comprehensive data on your inventory, including item codes, descriptions, quantities on hand, unit costs, and sales data. Ensure that the data is accurate and up-to-date.
2. Calculate Item Value
Calculate the value of each inventory item by multiplying the unit cost by the quantity on hand. This will provide an estimate of the value of each item in your inventory.
3. Rank Items by Value
Sort the inventory items in descending order based on their value. This ranking will help identify the most valuable items in your inventory.
4. Determine ABC Categories
Divide the inventory items into three categories based on their value.
Category A
This category consists of high-value items. It makes up a large part of the overall inventory. Usually, they only make up a small percentage of the total items but greatly impact inventory management and financial performance.
Category B
Items in this category have moderate value and importance. They are more numerous than category A items but still require attention and careful management.
Category C
C-category items have relatively low value individually. Still, they may represent a significant percentage of the total items in the inventory. Therefore, they have minimal impact on inventory management and financial performance.
5. Analyse Consumption Patterns
Study the consumption patterns and demand variability for each ABC category. This analysis will help you understand the characteristics and requirements of each category in terms of replenishment frequency, lead times, and order quantities.
6. Apply Different Inventory Management Strategies
Based on the ABC categorization, implement different inventory management strategies for each category.
Category A
Implement a more rigorous and proactive approach to managing these high-value items. This may include tighter control, frequent monitoring, and closer collaboration with suppliers to ensure availability and avoid stockouts.
Category B
Moderate-value items require a balanced approach with reasonable controls and monitoring. Implement strategies that optimise inventory levels while maintaining adequate availability.
Category C
Low-value items typically have a less critical impact on inventory management. Therefore, apply more relaxed controls and inventory management practices, focusing on cost-effective measures such as bulk ordering or vendor-managed inventory (VMI).
7. Regularly Review and Adjust
Inventory analysis is an ongoing process. First, regularly review and update your ABC categorization as market conditions, customer demands, and item values may change over time. Then, periodically reassess and adjust your inventory management strategies accordingly.
By using ABC analysis and applying appropriate inventory management strategies to each category, businesses can allocate resources, prioritize efforts, and optimize inventory levels.
This approach helps streamline operations, minimise costs, and improve customer satisfaction by ensuring the availability of critical inventory items while efficiently managing less crucial ones.
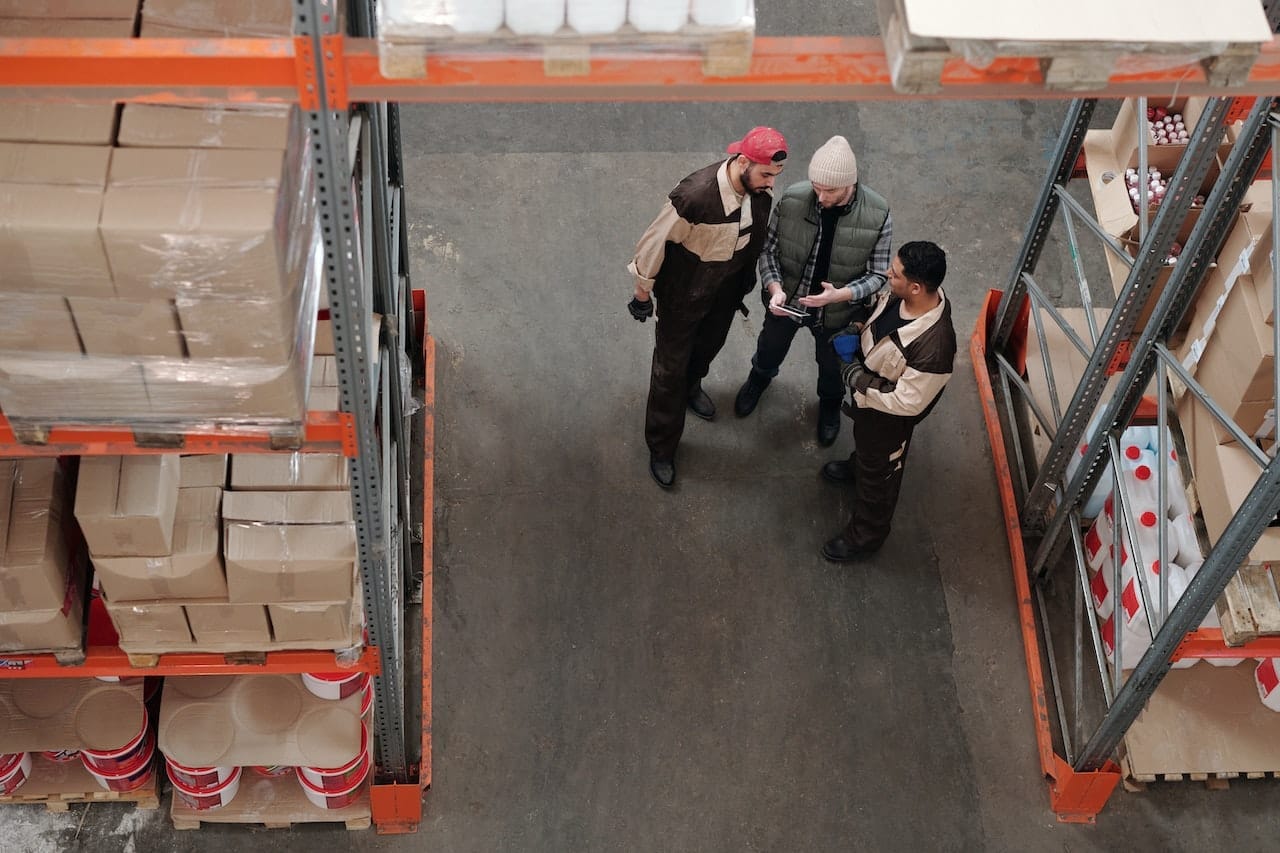
What are The 10 Inventory Strategies
Inventory strategies are approaches and methods used by businesses to manage their inventory effectively.
These strategies aim to balance meeting customer demand, minimizing costs, and optimizing operational efficiency. Here are some common inventory strategies
1. Just-In-Time (JIT)
JIT strategy focuses on minimizing inventory levels by ordering or producing goods just in time to meet customer demand. This approach reduces storage costs but requires precise demand forecasting and a well-coordinated supply chain.
2. Economic Order Quantity
EOQ strategy calculates the optimal order quantity by considering demand, ordering costs, and holding costs. It aims to balance reducing ordering costs (by ordering in larger quantities) and minimizing holding costs (by keeping inventory levels low).
3. Safety Stock
Safety stock strategy involves maintaining extra inventory to mitigate the risk of stockouts caused by unexpected demand fluctuations, supply chain disruptions, or lead time variability. In addition, it provides a buffer to ensure customer satisfaction and minimize lost sales.
4. ABC Analysis
ABC analysis categorizes inventory items into different groups based on their value or importance. Typically, items are classified as A, B, or C, where A items are high-value or critical items that require close monitoring. In contrast, C items are low-value or less critical.
This strategy helps prioritize inventory management efforts and allocate resources effectively.
5. Dropshipping
Dropshipping strategy involves partnering with suppliers who directly ship products to customers upon receiving orders. Businesses using this strategy do not need to maintain physical inventory, reducing inventory holding costs and the risk of unsold items.
6. Cross-Docking
Cross-docking strategy minimises the need for long-term inventory storage by immediately transferring incoming goods from suppliers to outbound transportation vehicles or customers. This approach eliminates the need for intermediate storage and speeds up order fulfillment.
7. Vendor-Managed Inventory (VMI)
In VMI, the supplier monitors and replenishes the inventory at the customer's location. As a result, the supplier can access real-time data and proactively ensure sufficient stock levels, reducing the customer's inventory management efforts.
8. Consignment Inventory
The consignment inventory strategy involves the supplier placing their products in the customer's facility or retail location. The ownership of the inventory remains with the supplier until it is sold. This approach reduces the customer's financial risk and inventory carrying costs.
9. Seasonal Inventory Planning
The seasonal inventory planning strategy is used when demand patterns vary significantly based on seasons or specific events. It involves adjusting inventory levels to meet the anticipated demand during peak periods and minimizing excess stock during slower periods.
10. Centralised vs. Decentralised Inventory
This strategy determines whether a business consolidates inventory in one central location or distributes it across multiple sites.
Centralized inventory reduces duplication and can result in economies of scale. In contrast, decentralized inventory improves response time and reduces transportation costs.
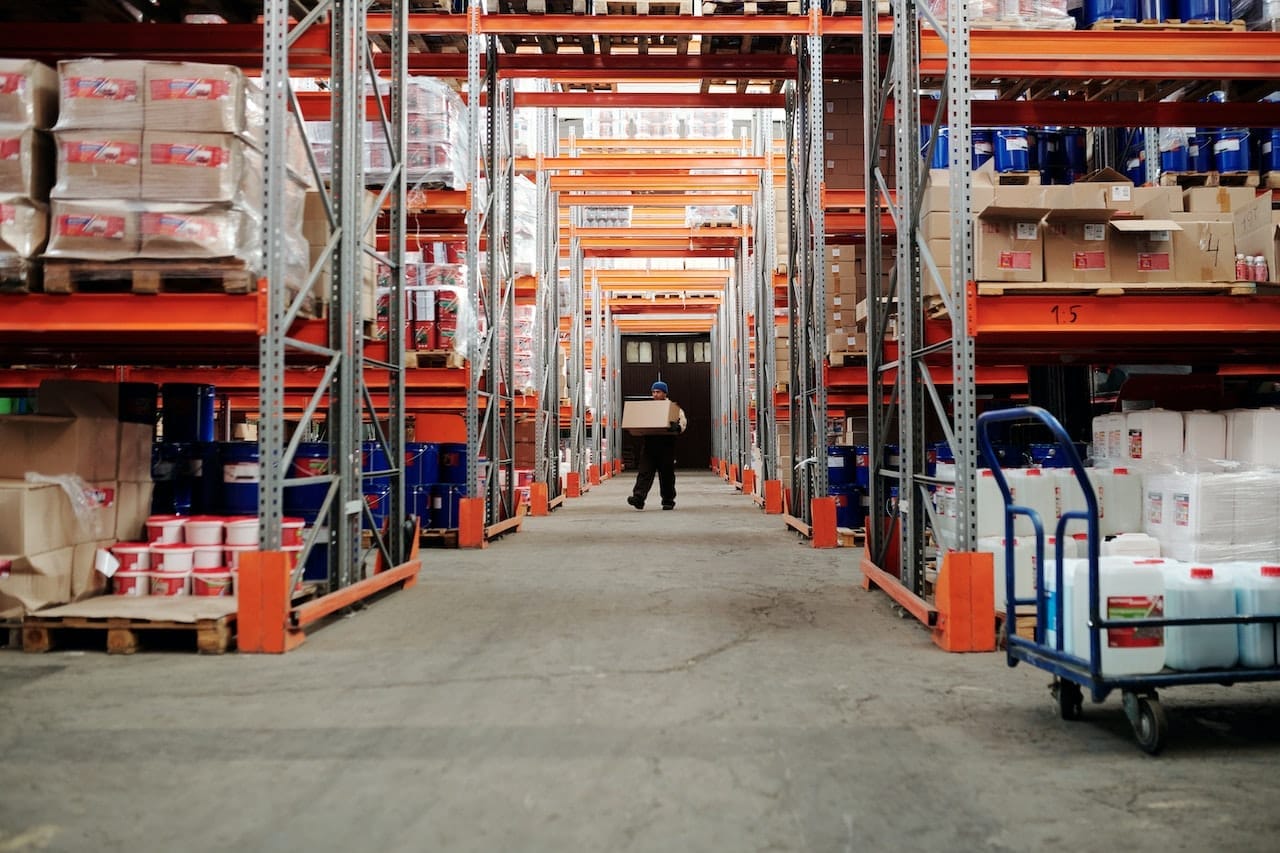
Conclusion
Inventory analysis is a crucial process for businesses seeking to optimize their stock. Companies can gain insights into its performance and financial impact by evaluating different aspects of inventory and utilising data analytics.
The article presents ten techniques for effective inventory analysis, including gathering accurate data, ranking items based on value, categorizing items using ABC analysis, analyzing consumption patterns, and implementing tailored inventory management strategies.
Regular review and key performance indicators further enhance inventory management. Additionally, the article highlights ten inventory strategies, such as JIT and dropshipping, that businesses can adopt to meet customer demand and minimize costs.