What is root cause analysis, the goal, and why is it important? Learn how to conduct a root cause analysis with the help of the 5 Whys and other techniques.
You might have heard someone saying, "this problem is deep-rooted" or "we have to find the root cause of this problem." But have you ever thought about what these phrases actually mean?
If you haven't thought about it yet, don't worry. Today's article will make you think critically and empower you with a tool to identify the root cause of any problem. Isn't that amazing?
You might be wondering what tool will enable you to identify the root of any problem. So, without making you curious, I'll tell you what tool I am talking about. Today I will introduce the Root Cause Analysis (RCA).
Root cause analysis is a tool business project managers use to solve various problems and identify their root causes.
In business, root cause analysis is used to identify and fix problems in processes, systems, or products and prevent similar problems from occurring.
One example of how root cause analysis is used in a business is the manufacturing industry, where it can identify the cause of product defects.
By understanding the root cause of the defects, manufacturers can take steps to improve their processes and prevent similar defects from occurring in the future. We have provided you with an overview of the root cause analysis. Let's proceed further and formally introduce you to this amazing problem-solving technique.
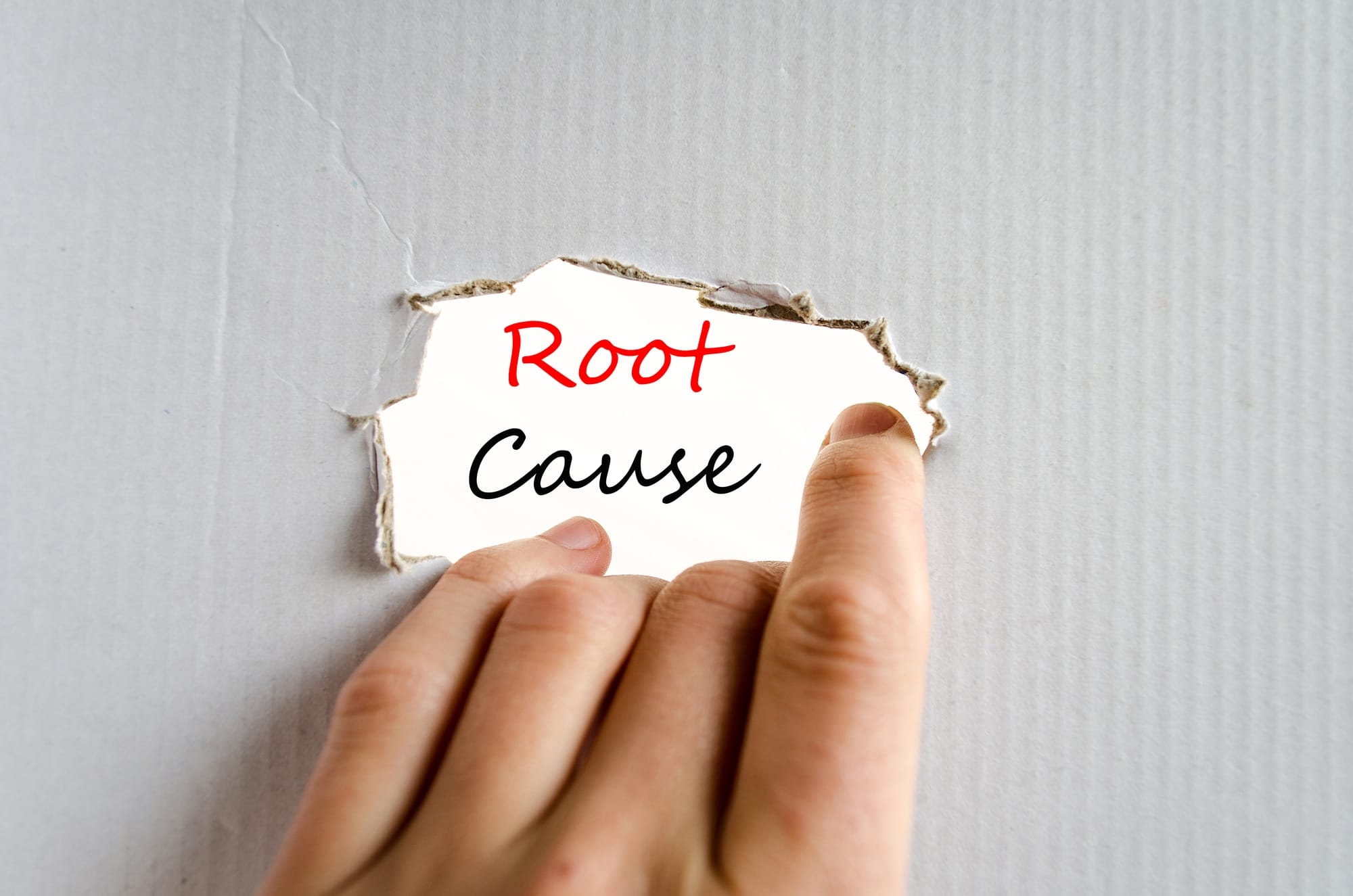
What Is Root Cause Analysis?
Root cause analysis is used to solve problems and identify the underlying cause of a problem or issue. Applying root cause analysis can save time, resources, and money. Moreover, it can improve efficiency, reduce costs, and increase customer satisfaction.
Root cause analysis can be used in various industries, including manufacturing, healthcare, and service, to improve efficiency, reduce costs, and increase customer satisfaction.
It can be applied to problems in processes, systems, or products. It can also help prevent similar problems from occurring in the future.
Several tools and techniques can be used in root cause analysis, such as the scatter diagrams, failure mode and effect analysis, and the "5 Whys" method, which involves asking "why" a problem repeatedly occurred until the root cause is identified.
Other methods include the fishbone diagram, which helps to identify potential causes for a problem, and the Pareto chart, which helps to prioritize actions based on their potential impact.
To effectively use root cause analysis, it is essential to involve a diverse group of stakeholders in the process, as different perspectives can help to identify the root cause more accurately.
It is also important to ensure that the root cause is thoroughly addressed rather than just addressing the symptoms of the problem.
Also, for reminiscence, it's important to mention that root cause analysis differs from the causal analysis, in which secondary or tertiary drivers of a certain challenge or problems are discussed, unlike RCA, where the focus is on the primary drivers.
What Is The Goal of Root Cause Analysis?
Before we jump on how to conduct the root cause analysis, you need to know what goal businesses expect to achieve by conducting root cause analysis.
The goal of conducting a root cause analysis is to highlight the root cause of a problem and take action to prevent it from occurring in the future. This may involve making changes to processes, systems, or products and require ongoing monitoring to ensure that the problem does not recur.
Businesses use root cause analysis to improve the overall quality of processes, systems, and products. By identifying and addressing the root cause of problems, businesses can ensure that their products and services meet the required standards and meet the needs of their customers.
This can increase customer satisfaction and loyalty and help businesses stand out in a competitive market. Root cause analysis can also identify and eliminate waste in processes, systems, and products.
Businesses can reduce costs and improve efficiency by identifying and addressing the root cause of problems that lead to waste. This can help businesses to stay competitive and improve their bottom line.
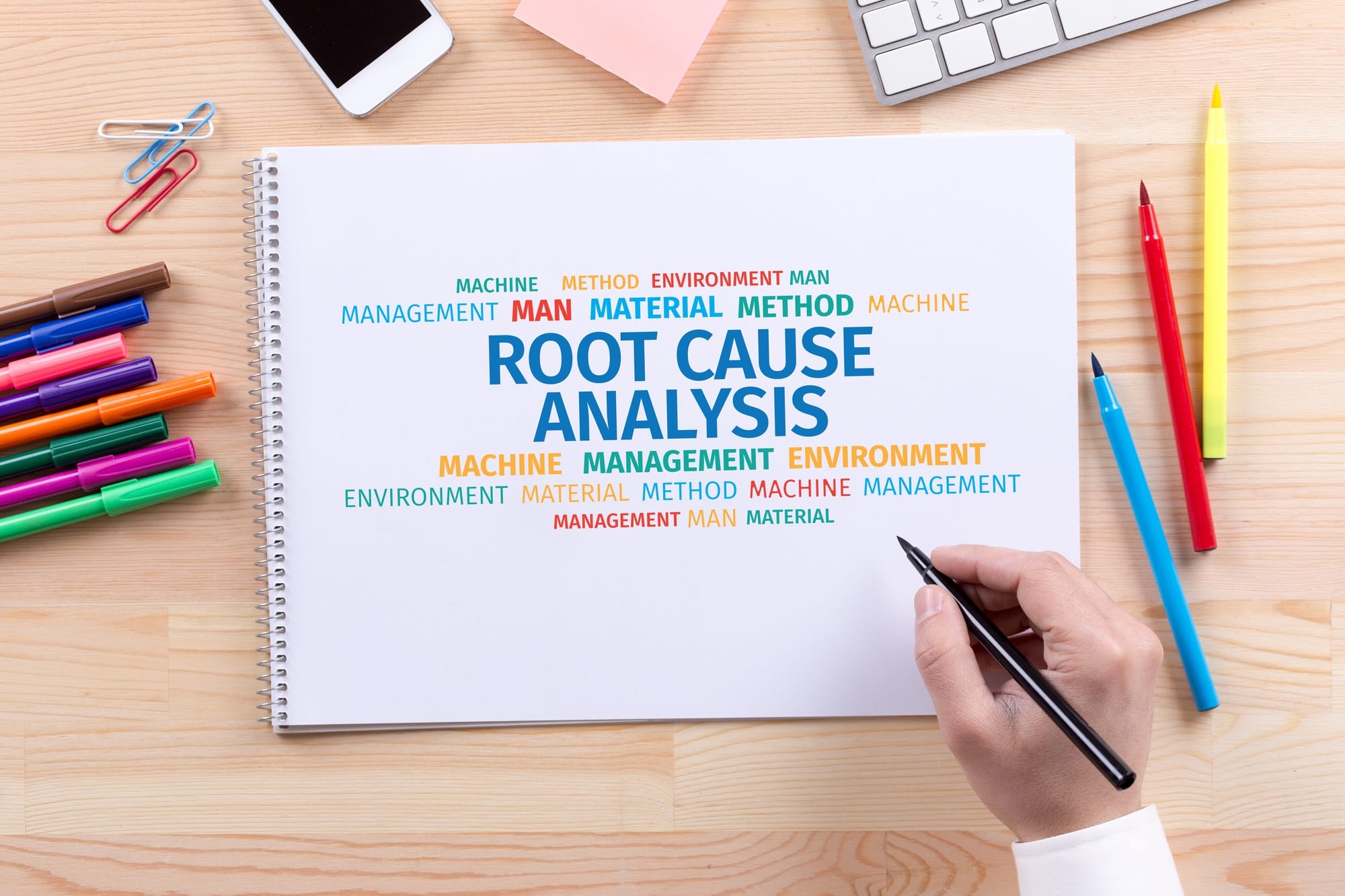
Why Is Root Cause Analysis Important?
Root cause analysis is a highly effective tool. It holds great significance for businesses and analysts working to mitigate the risks.
Root cause analysis is critical from a risk management perspective. By identifying and addressing the root cause of a problem, businesses can reduce the risk of similar problems occurring in the future. This can help businesses to mitigate potential risks and protect their reputation.
Moreover, businesses find the root cause analysis significant since it plays an essential role in increasing the efficiency of businesses, making them profitable.
For example, suppose a business is experiencing inefficiencies in its processes. In that case, it can use root cause analysis to highlight the root cause of the inefficiencies and take action to eliminate them.
This might involve streamlining processes, eliminating unnecessary steps, or improving the use of resources. As a result, the business can reduce the time and resources required to complete tasks by eliminating inefficiencies, leading to cost savings and increased productivity.
How To Conduct Root Cause Analysis?
We have already discussed the root cause analysis and why businesses use this technique. However, we haven't yet discussed how to conduct a root cause analysis. Therefore, this section is the most important section of this article since reading this will teach you how to conduct root cause analysis in six steps.
Identify The Problem
To begin root cause analysis, the first step is to examine the current situation and identify the factors contributing to the problem. By the end of this step, you must be able to identify the problem that is occurring.
For example, a business can generate less revenue than normal this year. By the end of this step, the business should be able to identify that it generated less revenue because its sales went down this year. This initial step aims to create a statement that clearly defines the problem at hand.
Data Collection Relevant To The Problem
Gathering relevant data about an incident or problem is essential to root cause analysis. This involves documenting the characteristics and details of the event, which can help to answer questions such as: What contributed to the problem? When did it occur? Does it happen repeatedly? What is the observed impact? By collecting this information, you can better understand the problem and take steps to prevent it from occurring again.
Highlighting Potential Causal Factors
A critical aspect of root cause analysis is creating a timeline of events to identify the factors that may have caused the observed problem. Therefore, the team conducting the analysis should work to establish a sequence of events and brainstorm as many potential causes as possible by asking "Why?" questions.
Tools like causal graphs can be helpful in visually representing the connections between events and tracking down the root cause. By following this process, you can better understand the factors that contributed to the problem and take steps to prevent it from occurring again.
Identifying The Root Cause
The analysis team can use techniques like the 5 Whys, Fishbone analysis, or Pareto chart to identify the most likely underlying cause or causes of the problem and the major contributing factors.
It is important to involve stakeholders and other relevant teams in this process to ensure that all relevant perspectives are considered. Using these techniques, you can narrow down the potential causes of the problem and move closer to identifying the root cause.
Prioritise The Root Causes
After identifying the root causes, it is essential to prioritize and address them most effectively. To determine which root cause to address first, the impact of each cause should be analyzed first. Then, the root cause with the highest impact should be given the highest priority.
Additionally, it is important to consider the number of causal factors triggered by a specific root cause - the more causal factors triggered, the greater the impact of the root cause and the more urgent it is to address it.
By prioritizing and addressing the root causes in this way, you can effectively address the problem and prevent it from occurring again in the future.
Providing a Solution
Once the root causes have been identified and prioritized, the next step is to find solutions to the problem and implement them. One of doing this is to brainstorm potential solution scenarios.
Another approach is gathering input from as many people as possible, as this can help generate various ideas and approaches. Finally, it is important to involve everyone in both the development and implementation of the solutions, as every recommendation counts, and successful implementation requires buy-in from everyone who will be affected.
By following this process, you can effectively address the problem and prevent it from occurring again.
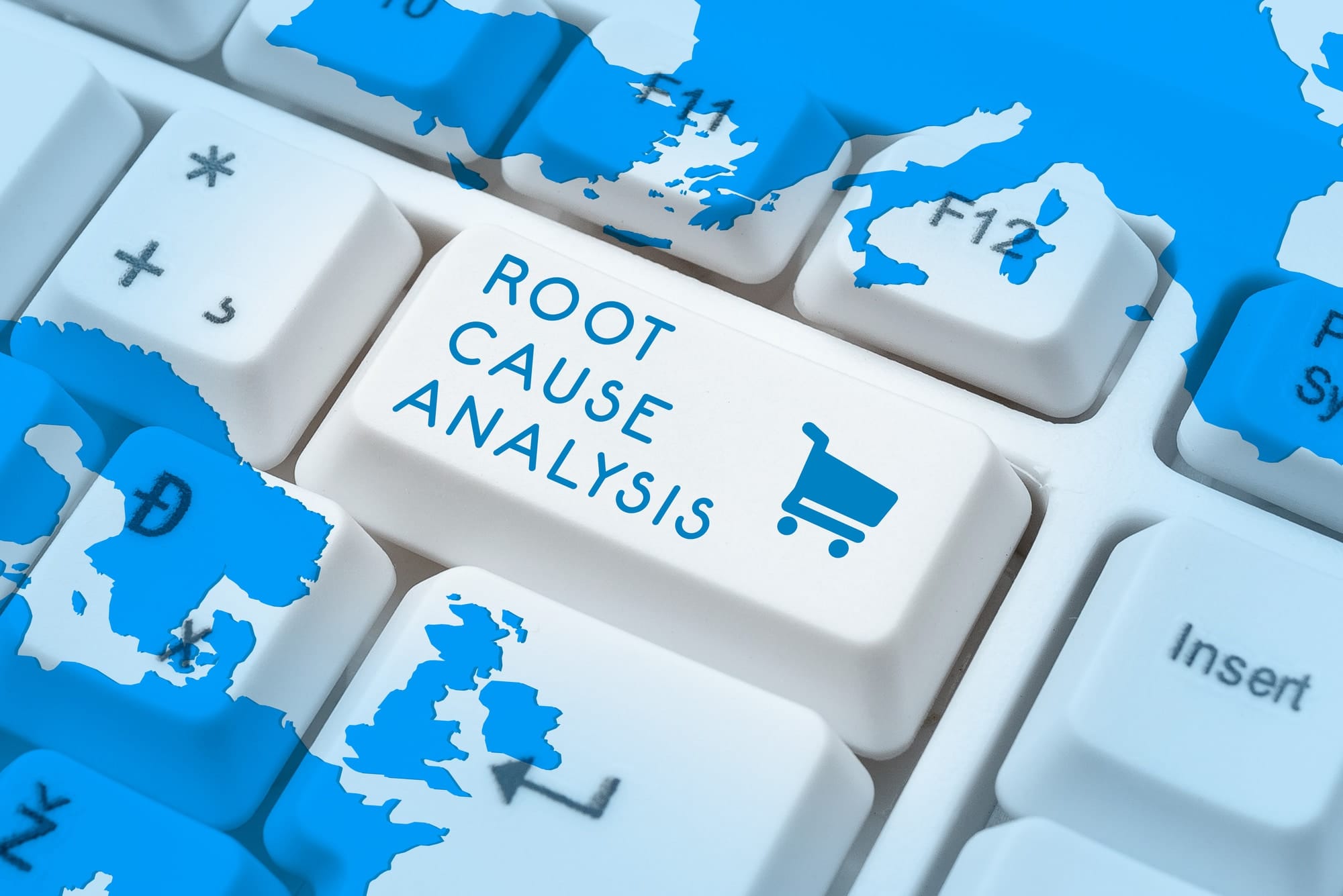
What Are The Methods To Conduct Root Cause Analysis?
Different methods can be used to conduct root cause analysis. Following, we have discussed some commonly used methods for conducting root cause analysis.
Pareto Charts
Pareto charts are useful for analyzing large amounts of production data quickly and easily. They display the most common sources of defects in descending order, making it easy to identify what areas will have the greatest impact if improved. By using Pareto charts, teams can prioritize their efforts for maximum effectiveness.
Fishbone Diagrams
Fishbone Diagrams, also called Cause-and-Effect Diagrams, help identify the potential causes of a problem that can be grouped into different categories.
This technique is especially useful when the root cause of a problem is unknown. Using a Fishbone Diagram, you can systematically consider different categories of potential causes and work towards identifying the root cause of the problem.
The 5 Whys
The 5 Whys is a useful investigative technique that can help process engineers conduct root cause analysis by identifying the core reason why an event occurred. This method involves repeatedly asking "Why?" questions until the problem's root cause is identified.
The 5 Whys is particularly effective when investigating simple problems that don't require detailed quantitative analysis.
Scatter Diagrams
Scatter Diagrams are the graphs used to show the relationship between two data sets. For example, to use a scatter plot as a root cause analysis tool, you would plot both variables on the axis.
If there is a clear pattern when you plot these two variables, you may suspect that they are correlated. Using a scatter plot, you can identify potential correlations between different variables and use this information to help identify the root cause of a problem.
Failure Mode and Effect Analysis
Failure Mode and Effect Analysis (FMEA) is a tool that can be used to identify and examine all the potential points of failure in a design, process, or product, as well as the possible consequences of those failures.
This technique typically involves a cross-functional group of stakeholders who know about the design, process, or product and can help document potential root causes before they occur. FMEA can be used at any production stage to help identify and prevent potential problems.
By using this tool, you can take proactive steps to improve the reliability and effectiveness of your designs, processes, or products.
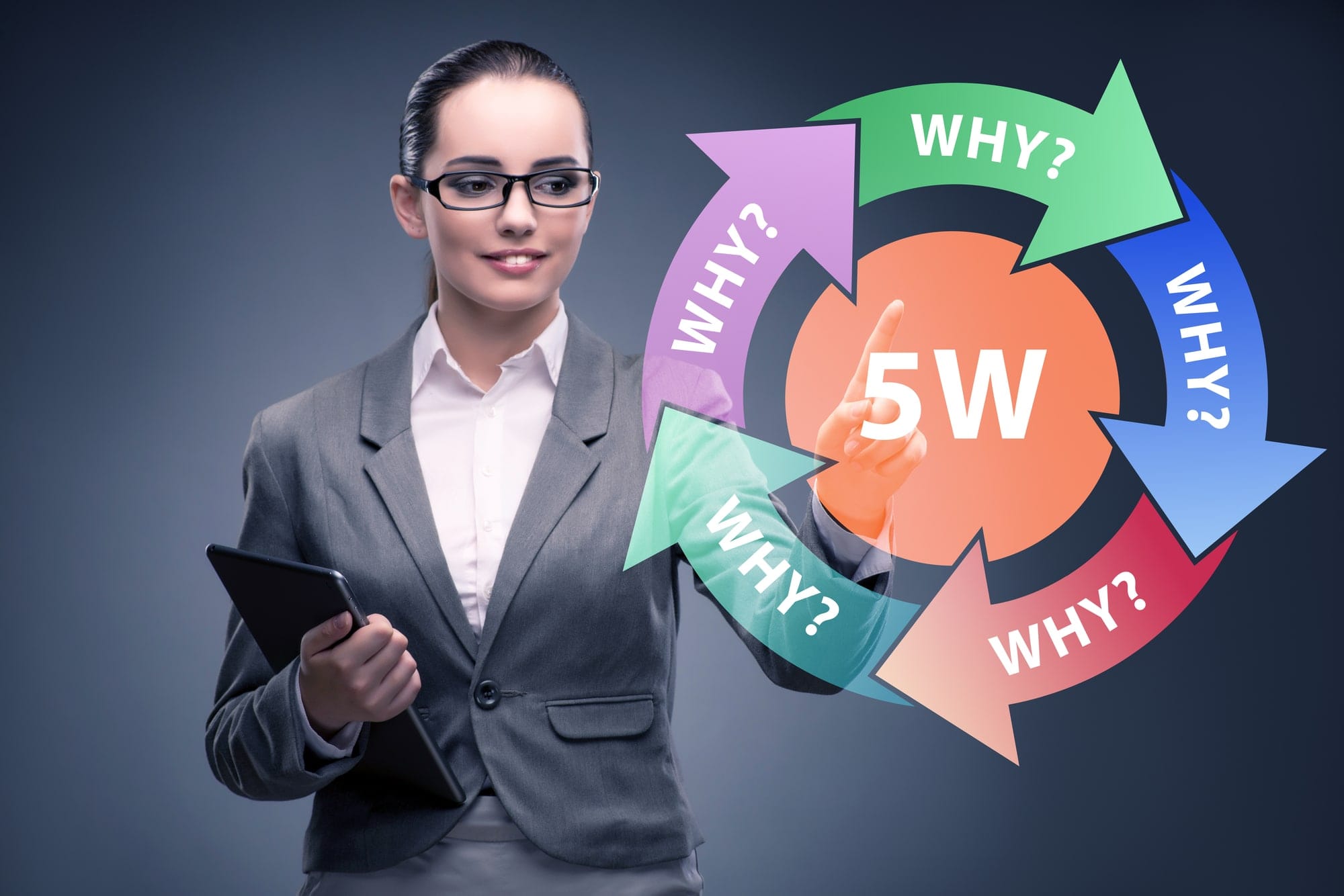
What Are The 5 Whys of Root Cause Analysis?
The 5 Whys is a root cause analysis technique that involves repeatedly asking "Why?" to identify the root cause of a problem. The idea is to keep asking, "Why?" until you know the root cause of your problem.
For example, if you are a supervisor in a manufacturing plant trying to identify the root cause of a machine breakdown, you might ask:
Why Did The Machine Break down?
The answer you will get from this question would be "because a part of the machine failed." This answer will lead you to the second question that will be:
Why Did The Part Fail?
The answer to this question will be "because it was worn out." This answer will take you to the 3rd why:
Why Was The Part Worn Out?
This question will be answered like this" Because it was not replaced when it should have been." This will raise a new question that will be:
Why Was The Part Not Replaced?
The reason why the part wasn't replaced would be "Because the maintenance schedule was not followed." Answer to the last this question will lead you to the last why that is:
Why Was The Maintenance Schedule Not Followed?
The answer is "the maintenance team was understaffed and did not have the time to complete all necessary tasks." The answer to the last why will help you reach the root cause of the problem.
If we look at this example, we know that the manufacturing machine broke down because the maintenance team was understaffed and did not have the time to complete all necessary tasks using the 5-why technique.
Root Cause Analysis: Final Word
Root cause analysis is a problem-solving technique businesses use to highlight the factors causing the problem. This technique helps businesses become more profitable and productive because it ensures they don't suffer again because of the same problem.
This article made you realize the importance of root cause analysis and discussed its significance. Then it taught you how to conduct the root cause analysis in 6 steps.
After that, we discussed the methods of conducting the root cause analysis and finally took a look at the 5-why technique used to conduct a root cause analysis. In the end, we hope you would have enjoyed reading this article. After reading it, you must have learned how to conduct a root cause analysis.