The Business Process Analysis evaluates various steps that show how a business operates, with the aim of identifying inefficiencies or areas for improvement.
Imagine you are a business analyst of a top-notch company who has to see if the business is operating well. What is that one analysis that will provide you with an overview of the entire operation and paint a picture of what is going well and what needs to be fixed?
You might be wondering if such a technique exists or not. Well, what if I tell you it does? The Business Process Analysis evaluates various steps and procedures that show how a business operates, with the aim of identifying any inefficiencies or areas for improvement. It involves a thorough analysis of each aspect of a business process to know what is functioning well and what could be improved.
There are various techniques for conducting business process analysis. Still, the ultimate goal is to optimize the system to achieve better overall business outcomes.
There are several reasons why businesses use business process analysis. One of the main reasons is to increase efficiency and reduce costs.
Businesses can streamline their processes and improve quality, speed, and overall performance by identifying bottlenecks or areas where errors occur. This can lead to cost savings, while it can also improve customer satisfaction and loyalty.
Another reason businesses use business process analysis is to identify new opportunities for growth and innovation. By examining how a business operates, it is possible to identify new ways of doing things that may not have been considered before. This can lead to the development of new products or services, as well as the expansion of existing ones.
Business process analysis is also used to improve compliance with regulations and industry standards. By examining and redesigning processes, businesses can ensure that they meet all necessary requirements and avoid costly fines or penalties.
After reading this, I am sure you are now aware of business process analysis. So let's proceed further and take a look at some of the business process analysis tools that are widely used in business process management.
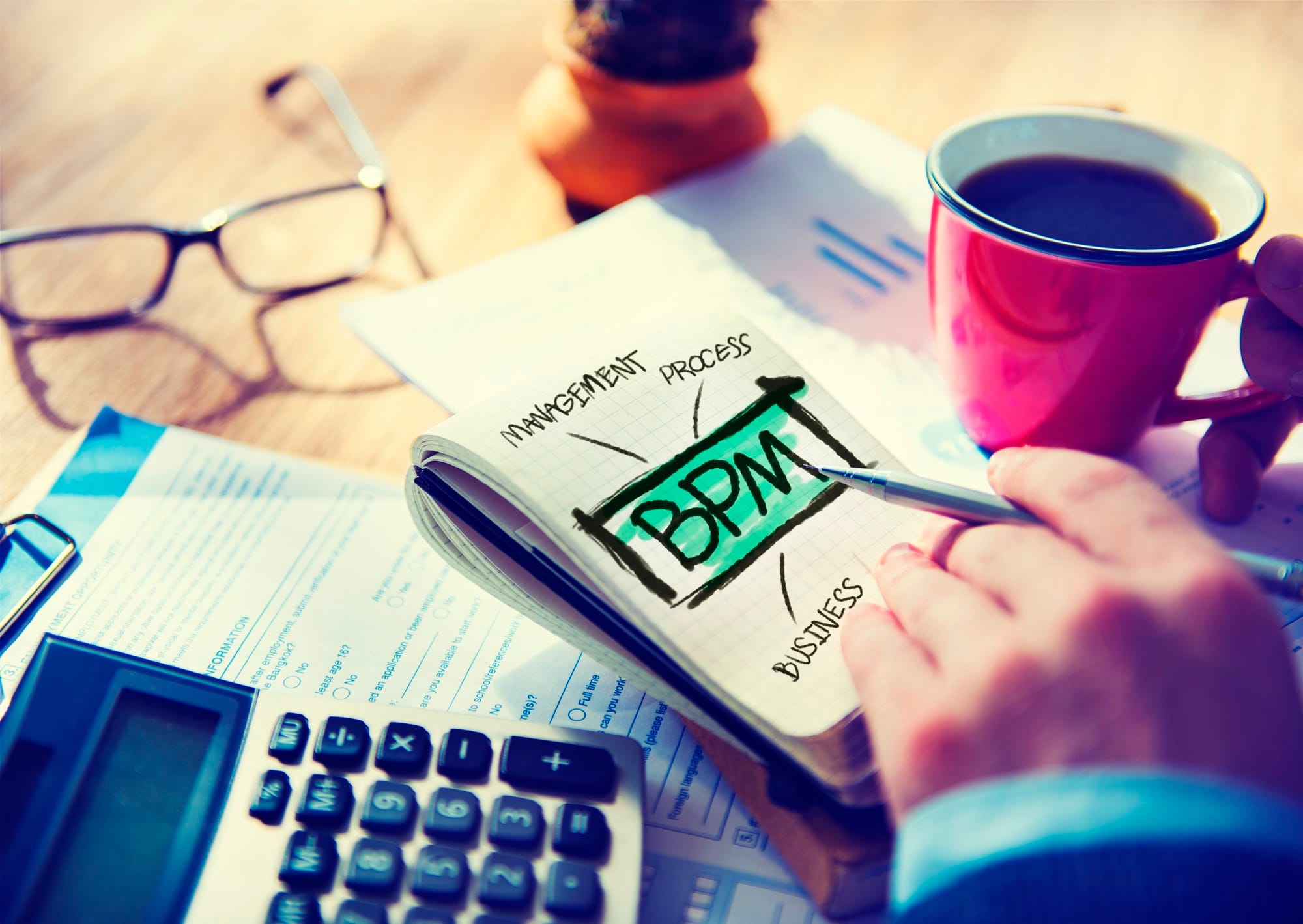
Business Process Analysis Tools
There are various tools available for identifying and addressing the inefficiencies of businesses. The selection of tools depends on an individual or team's specific needs and objectives. Let's look at what business process analysis tools can help conduct the analysis.
Six Sigma
Six Sigma is a methodology for improving business processes by identifying and eliminating defects and variability. It is a data-driven approach that utilizes statistical analysis and problem-solving techniques to identify the root causes of problems and implement solutions that achieve near-perfect performance.
Six Sigma is typically used to improve processes critical to an organization's success, such as manufacturing, finance, or customer service. In addition, it is often used to address specific problems or inefficiencies, such as defects in a product, delays in a process, or customer complaints.
The Six Sigma approach involves a systematic, data-driven process known as the DMAIC (Define, Measure, Analyze, Improve, and Control) method. The initial step is to define the problem or opportunity for improvement and set specific, measurable goals. Next, data is collected and analyzed to identify the root causes of the problem.
Based on this analysis, improvement solutions are developed and implemented. The process is monitored and controlled to ensure that the improvements are sustained over time.
Six Sigma is often used with other tools and techniques, such as process mapping, root cause analysis, and statistical process control. However, it is a highly structured approach that requires a high investment of time and resources. Still, it can significantly improve quality, efficiency, and customer satisfaction.
Lean Six Sigma
Lean Six Sigma is a methodology that mixes the principles of lean manufacturing and Six Sigma to improve efficiency and eliminate waste in business processes. Lean manufacturing is a methodology that focuses on reducing waste and increasing efficiency by streamlining processes and eliminating non-value-added activities.
While Six Sigma is a methodology for improving business processes by highlighting and eliminating defects and variability, as we discussed earlier, Lean Six Sigma combines both of these approaches to create a highly efficient and effective process improvement methodology. It involves identifying and eliminating waste and variability while focusing on continuous improvement and customer satisfaction.
The Lean Six Sigma approach involves a systematic process known as the DMAIC (Define, Measure, Analyze, Improve, and Control) method, similar to the Six Sigma approach. By combining the principles of lean manufacturing and Six Sigma, organizations can increase efficiency and improve their quality, which will benefit them.
Continuous Improvement (Kaizen)
Continuous improvement, or Kaizen, is a philosophy and approach that focuses on making small, incremental changes to improve efficiency and effectiveness over time.
It involves a continuous cycle of identifying opportunities for improvement, making changes, measuring the results, and making further improvements based on the results.
Kaizen aims to remove three types of waste:
- Muda: Muda is waste that does not add value to the product or service provided. This can include unnecessary steps in a process, excess inventory, or defects.
- Mura: Mura is waste that results from inconsistencies or variations in a process. This can include variability in demand, production, or quality.
- Muri: Muri is waste that results from overburdening employees or resources. This can include overproduction, overprocessing, or over-reliance on overtime.
By identifying and eliminating these types of waste, organizations can streamline their processes and improve efficiency and effectiveness. Furthermore, by applying the continuous improvement philosophy of Kaizen, organizations can foster a culture of continuous learning and improvement and achieve ongoing, incremental improvements over time.
Lean Manufacturing
Lean manufacturing is a production system that aims to minimize waste and maximize value by streamlining and optimizing production processes. Lean manufacturing aims to create customer value by producing high-quality products efficiently and cheaply.
There are five principles of lean manufacturing:
- Identify value: What the customer values in a product or service, and focus on delivering that value.
- Map the value stream: Identify all the steps in the production process, and eliminate any that do not add value for the customer.
- Create flow: Design the production process to minimize interruptions and delays so that work can flow smoothly and efficiently.
- Establish pull: Implement a system in which work is only started when needed, rather than working on a fixed schedule or producing more than is needed.
- Seek perfection: Continuously improve production by identifying and eliminating waste and inefficiencies and making small incremental improvements over time.
Total Quality Management
Total Quality Management (TQM) approach seeks to improve the quality of products and services by engaging all employees in a continuous process of identifying and eliminating defects and variability in all business processes.
TQM is based on the belief that quality can be improved by involving all employees in the quality process and empowering them to identify and solve quality problems.
The key features of TQM include the following:
- Customer focus: TQM places the customer at the center of all business activities and aims to deliver high-quality products and services that meet or exceed customer expectations.
- Continuous improvement: TQM encourages a culture of continuous improvement in which all employees are actively involved in identifying and solving problems to improve the efficiency and effectiveness of business processes.
- Employee involvement: TQM involves all employees in the quality process and empowers them to identify and solve quality problems.
- Process-oriented approach: TQM focuses on producing and delivering products and services rather than just individual steps or tasks.
- Data-driven decision-making: TQM uses data and metrics to measure business processes' performance and identify improvement areas.
- Leadership: TQM requires strong leadership at all levels of the organization to create a culture of continuous improvement and to ensure that TQM practices are consistently applied.
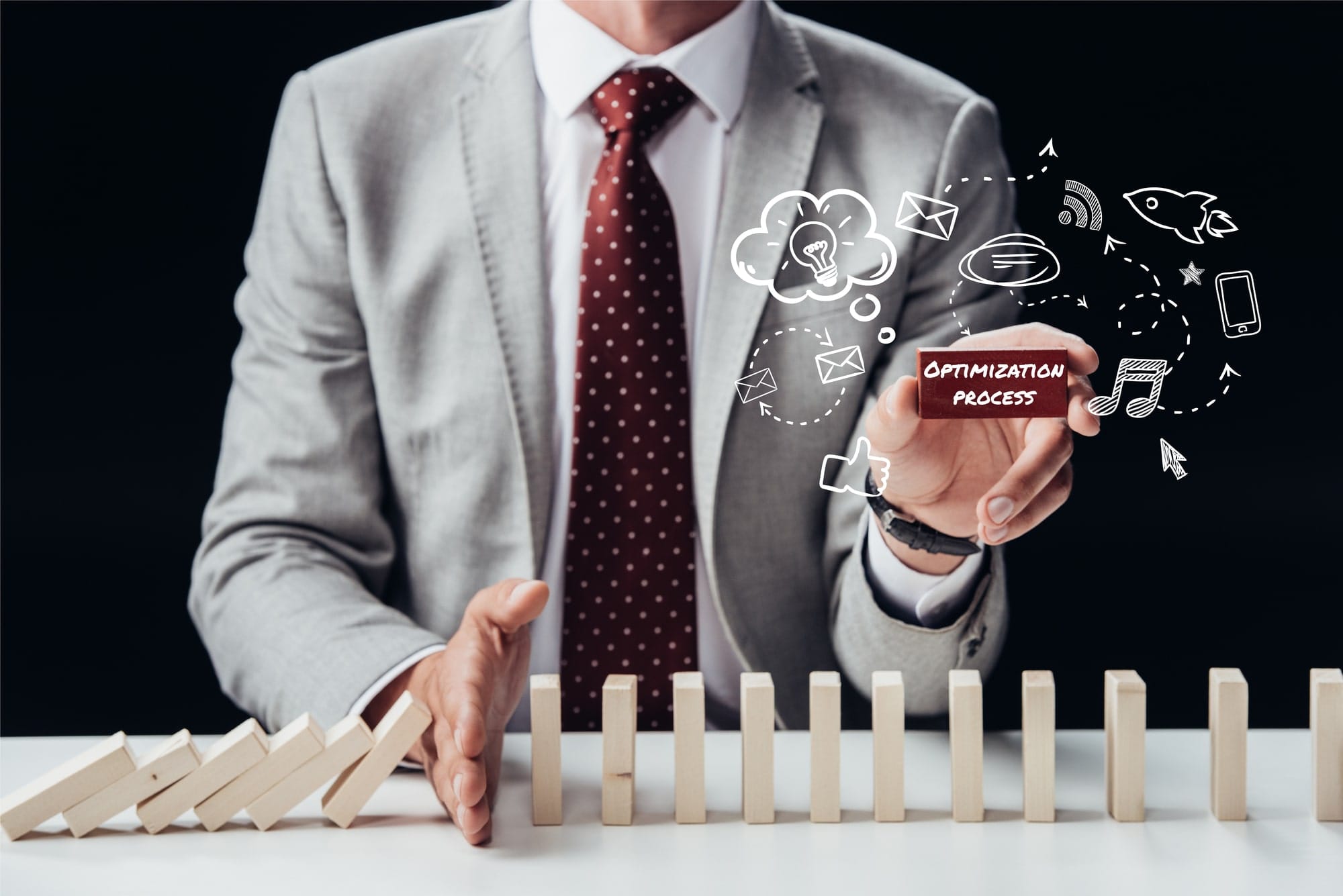
Business Process Analysis Examples
We have already discussed what business process analysis is. However, to ensure that you get a better understanding, it is important to provide you guys with some business process analysis examples.
Example: Imagine a business analyst analyzing his company's hiring process. The business analyst will begin by mapping out the current hiring process to identify the steps involved and the time it takes to complete each step.
He will then identify bottlenecks or inefficiencies in the process, such as a lengthy review process or a lengthy background check process.
To address these issues, the business analyst will implement several changes to streamline the process. For example, he will introduce an automated applicant tracking system to reduce the time it takes to review resumes and schedule interviews.
The business analyst will also introduce a more efficient background check process or outsource the background check process to a third party.
In addition, the business analyst might suggest indulging HR staff and hiring managers in training to improve the process, in which they regularly review and analyze the hiring process to identify further opportunities for improvement.
By applying business process analysis to the hiring process, the business analyst can significantly reduce the time a company takes to fill open positions and improve the efficiency of the overall process. This can ultimately lead to cost savings and improved competitiveness for the company.
Example 2: In this example, a project manager conducts the business process analysis to see whether the project planning is going well.
The project manager will analyze each stage of the current project planning process to identify the steps involved in planning. For example, the project manager might identify problems, such as a lengthy resource allocation process.
To counter the identified problem, the project manager might introduce an automated project management software tool to help with task scheduling and resource allocation. In addition, he might introduce a more efficient system for reviewing and approving project plans.
Moreover, the project manager might involve all stakeholders in a continuous improvement process, in which they regularly review and analyze the project planning process to identify further opportunities for improvement.
This will help the project manager to correct the problems in the project planning in the initial stages before they get out of hand.
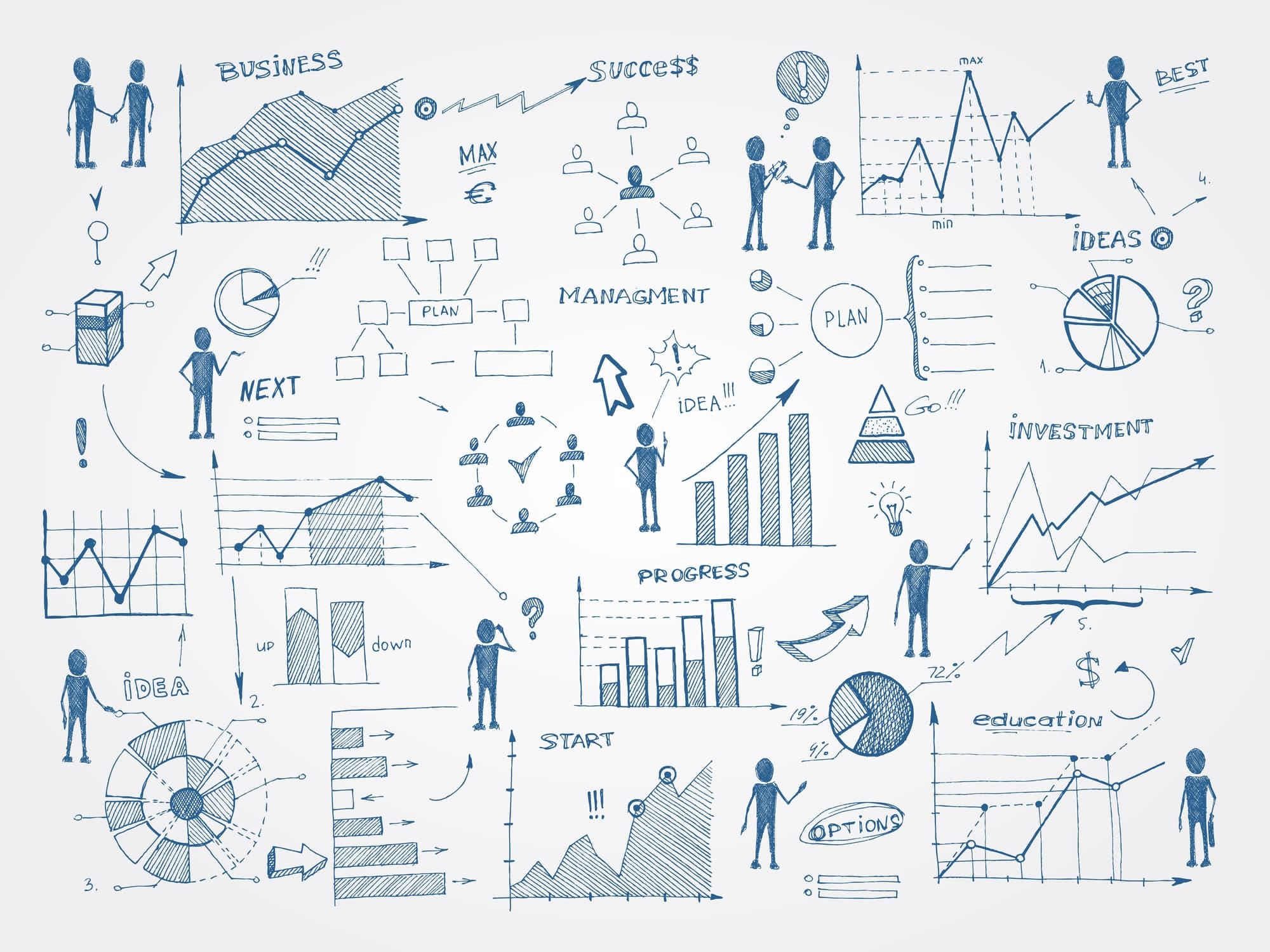
Business Process Analysis Model
You are fully aware of the purpose and significance of business process analysis. So let's proceed further and discuss the stages that enable the business process analysis.
Define The Scope of The Analysis
Defining the scope of the analysis is an essential first step in conducting a business process analysis. The scope of the analysis should clearly define the business process that will be analyzed, as well as the specific goals or objectives of the analysis.
Defining the scope of the analysis helps to focus the analysis on the specific areas that need improvement and helps to ensure that the resulting improvements are aligned with the needs and goals of the organization.
It also helps to ensure that the analysis is conducted systematically and organized and that all relevant stakeholders are involved in the process.
Gather Data
Gathering data is an important step in conducting a business process analysis. To gather data on the current state of the business process, organizations can use various tools and techniques, such as interviews, surveys, process maps, and data analysis.
Gathering data on the business process's current state helps organizations understand how the process currently works and identify opportunities for improvement. Therefore, gathering as much data as possible is essential to ensure that the analysis is thorough and accurate.
Map The Process
Mapping the process is a key step in conducting a business process analysis. Organizations can better understand how the process works and identify bottlenecks or inefficiencies by creating a visual representation of the business process.
There are several tools that organizations can use to map the business process, such as flowcharts, process maps, and swimlane diagrams. These tools can help to visualize the steps involved in the process, the resources used, and the flow of work.
Identify Areas For Improvement
There are several approaches that organizations can use to identify areas for improvement, such as identifying steps that take a long time to complete or add little value.
For example, a company might analyze the order fulfillment process to identify steps that take a long time to complete, such as picking and packing products. The company might then identify opportunities to streamline or eliminate these steps to improve the efficiency of the process.
By identifying areas for improvement, organizations can focus on addressing the root causes of problems or inefficiencies and can make targeted improvements to the business process to deliver value to customers and improve the organization's overall performance.
Develop Improvement Ideas
After identifying areas for improvement in a business process, the next step is to develop improvement ideas. This involves brainstorming potential solutions to the identified problems and evaluating each idea's potential benefits and costs.
Once potential improvement ideas have been identified, it is essential to evaluate each idea's potential benefits and costs. This can help organizations to prioritize their improvement efforts and to select the most promising ideas for implementation.
Factors to consider when evaluating improvement ideas might include the potential impact on the business process, the resources required to implement the idea, and the potential return on investment.
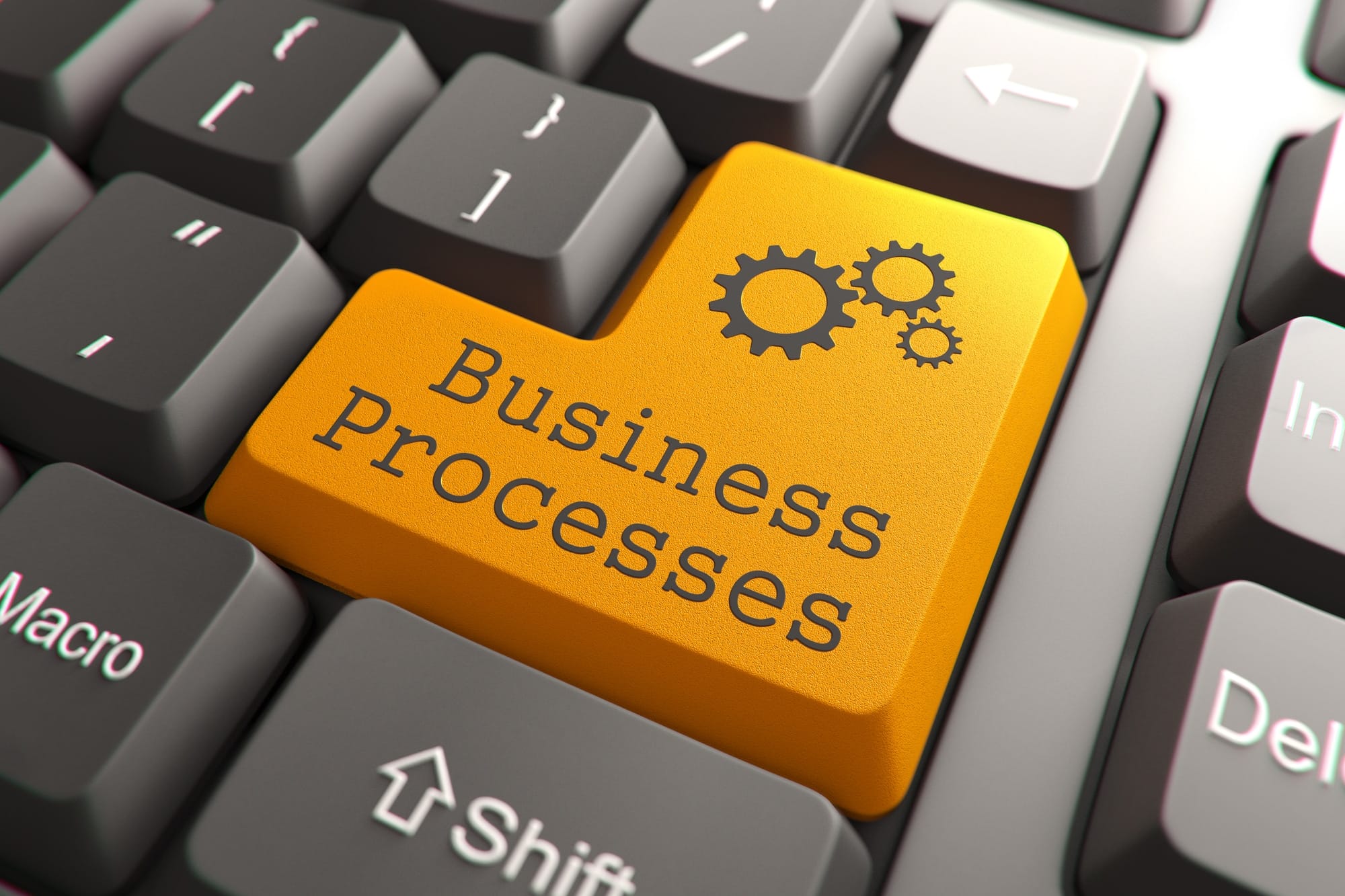
4 Steps for the Business Process Analysis Planning
Business analysts are in charge of continuous projects. The start of a new one can have even the most seasoned analyst sweating. After all, expectations shift, results are always necessary, and success is the primary objective.
The business process analysis can help with new projects in fast-moving environments. While the complexity of projects fluctuates, the right process can help you find your ground and get the project moving in the right direction.
Take Time
You may find yourself in the middle of a project and are expected to start immediately. It won’t be long until you feel like you’re overwhelmed. That’s when the panic sets in.
But you must ensure you’re not moving quickly. Take time — hours, days, or weeks if you can — to truly understand this project. Now that you’re in charge of the project, you want to clarify the expectations company leaders have.
If possible, research and understand the project. Who initiated it? Were there other analysts working on it before you? What data had they already used? It’ll be up to you to understand which processes were previously set in place and how you can utilize them to your advantage.
Remember, getting settled means collecting relevant information before you get started.
Understanding objectives
The plan involves goals set by stakeholders and leaders within the company. It’s time to find out what they are. This has to be understood early in order to make smart decisions for the project later on. If you’re not on the same page as the stakeholders, the project may be doomed.
Address expectations. What are stakeholders expecting from this project? Does it match up with what you were told when the project was given to you? And ensure the objectives are clearly defined, without room for interpretation.
Interpretation leads to misunderstanding, which can lead to project failure.
Scope and responsibilities
Next is determining scope. This means setting boundaries within a business and assigning responsibility to team members. The point is to keep everyone focused and on track.
Each member, including yourself, will see the objectives. You can create a scope document or statement to send to stakeholders or leaders. They may require signing off on it before work begins. It’s best to do this to ensure everyone understands the project and what is expected of them.
This is not the business plan. It’s the step before the project is formulated. The scope is used to define needs and roles and ensure everyone understands what to expect. When this is agreed upon, the planning stage commences.
Business analysis plan initialization
The plan is essential in any business process analysis. It will highlight requirements and address possible questions by team members, stakeholders, and leaders. The previous step, scope setting, will help with this step.
By understanding the process, business requirements, and key aspects, you will select the tooling used to complete the project. This includes strategic planning, analysis, and framework design.
You’ll also address the timeline and periodic goals. Specifically setting weekly, monthly, or bi-monthly goals. You’ve outlined which deliverables are necessary, but the due date must be set as well.
A detailed plan may not be possible, but lists of expectations can be. This can also suffice as a plan for the time being.
Here, you’ll go into great detail about deliverables, methods to meet objectives, team member roles, and expectations. It will help you create solutions for the corporation to implement.
By following these steps of the business process analysis, you’ll have the outline to create a plan that will benefit company objectives. Remember to start slowly so you can understand needs, grasp objectives, set scope and regulations, then begin the planning process.
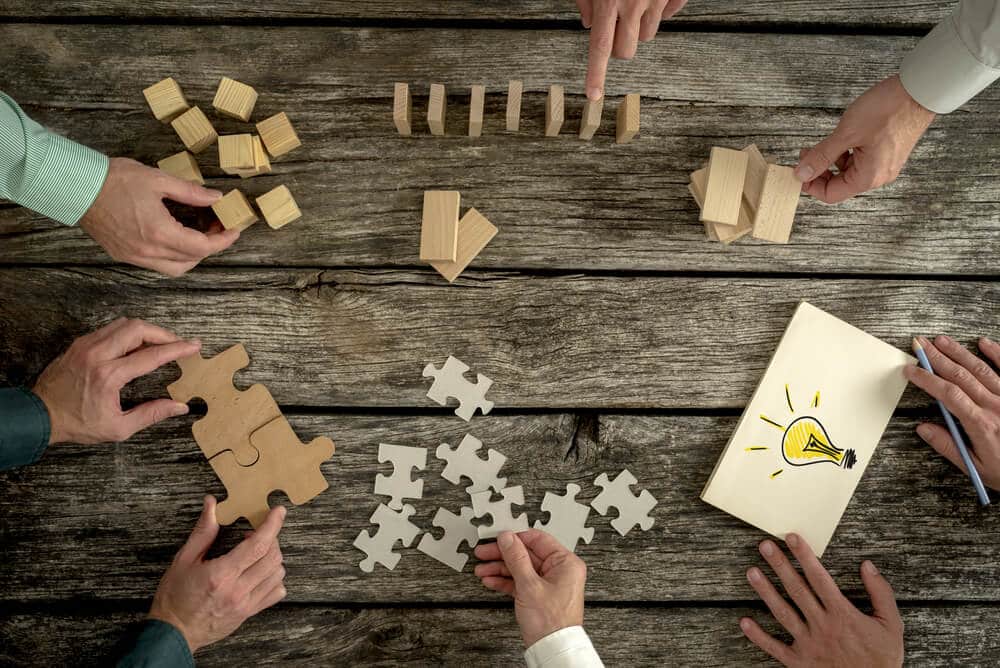
Business Process Analysis: Final word
Business process analysis systematically examines and improves an organization's business processes. The business process analysis aims to identify and eliminate waste and inefficiencies and continuously improve the efficiency and effectiveness of business processes.
This can help organizations deliver value to customers, reduce costs, and improve the organization's overall performance.
Business process analysis typically involves several steps, such as defining the scope of the analysis, gathering data on the current state of the business process, mapping the process, identifying areas for improvement, and developing improvement ideas. By conducting a thorough business process analysis and implementing improvements based on the findings, organizations can significantly improve the efficiency and effectiveness of their business processes and drive long-term success.